Voron 2.4 R2: путь джедая
Приветствую, уважаемый читатель! В этой статье я постараюсь поделиться своим опытом по созданию 3D-принтера по проекту VoronDesign. Но, для начала, расскажу своими словами что это такое и для чего это нужно.
VoronDesign - это сообщество профессионалов и энтузиастов, работающих над open-source проектами по созданию 3D-принтеров. Прежде всего, их принтеры отличаются от других несколькими существенными моментами:
1) Крутой дизайн: красиво, лаконично и завершенно. Чувство, что работали профессионалы с большой буквы присутствует.
2) Необычные, эффективные и продуманные до мелочей технологические решения.
3) Упор на общедоступные компоненты
4) Активное и развитое сообщество
5) Открытый исходный код! Доступны все CAD файлы, схемы и исходный код для модификаций.
Теперь про сам принтер: Voron 2.4 R2.
1) область печати - выбираешь сам, все кастомизируемо. От 100х100х100, до 1000х1000х1000 и более, вопрос лишь в здравом смысле.
2) Кинематика CoreXYZ. Опечатки здесь нет: не CoreXY, а CoreXYZ. Стол у этого принтера неподвижен, зато по оси Z движется каждый из четырех углов гентри, вместе с хотендом! Много ремней, много моторов. Сложно, но невероятно красиво и захватывающе во время работы.
3) Железо управляется универсальной платой Octopus. Богатый функционал, 32bit, обилие портов ввода-вывода.
4) Микрокомпьютер на RaspberryPi \ Orange PI (Klipper + Mainsail\Fluidd). Рекомендую брать одноплатник с возможностью подключения SPI (мой выбор - Orange Pi PC Plus)
5) По умолчанию - пассивная термокамера, но истинные джедаи выбирают активную с регулируемой циркуляцией
6) Множество вариантов подключения веб-камер
7) Тонны уже готовых модов и аддонов, полезных и не очень, что бы вдумчиво разобраться во всем этом многообразии, потребуется не один день. Если есть идея для модификации - прежде чем воплощать ее в CADe, верным решением будет поиск на VoronUsers.
8) Китайцы бодро подхватили идею и стали делать готовые наборы для сборки: 200х200х200, 250х250х250, 300х300х300, 350х350х350. Наборов для сборки с бОльшим размером я не нашел, но если хочется 500х500х500 - придется самостоятельно пилить профили, резать оргстекло, дорабатывать пластиковые юбки и фрезеровать алюминиевую пластину для стола, на этот случай, прямо на сайте есть конфигуратор будущего принтера - указываешь желаемые размеры, получаешь BOM в xls.
Все это очень круто, но ровно до тех пор, пока не приходит осознание, что все нужно собирать, выбирать, настраивать, прошивать и калибровать САМОСТОЯТЕЛЬНО! Каждый болт, каждый компонент, каждый провод. Устанавливать линукс, разбираться с компиляцией прошивки и сборкой из исходников.
Еще один важный момент - все пластиковые части надо печатать на ДРУГОМ принтере, но, китайцы и тут подсуетились и за дополнительную плату готовы предложить набор из пластиковых деталей.
Итак. Вы прониклись. Вдохновились. Подумали. Решились.
Спешить не надо, на следующий день, а лучше через три - еще раз подумайте, хватит ли вам сил, терпения и навыков пройти весь этот путь СОЗДАНИЯ своего собственного Ворона от начала и до конца.
Результатом будет не только топовый 3Д-принтер, но и новые знания и навыки, которые поднимут понимание технологии 3Д-печати на новый уровень.
В начале пути, юного падавана ждет выбор комплекта для сборки. Мой выбор пал на комплект от Formobot 350x350x350. Все компоненты высочайшего качества. Raspberri в комплекте нет, пластиковых деталей тоже - заказываются отдельно.
Мой комплект шел около месяца. За это время, рекомендую вам, как минимум, начать печатать пластиковые детали (уйдет несколько килограммов пластика) и хорошо изучить документацию по сборке, настройке и калибровке. Мелочей - бесчисленное множество, но все очень хорошо задокументировано и при СТРОГОМ следовании материалам все получится.
Не спешите радоваться, когда получите уведомление о прибытии груза. После открытия коробки, вас ждет набор хорошо упакованных компонентов для ВДУМЧИВОЙ, медленной и тщательной сборки. Этот формат принтеров сильно отличается от привычного: распаковал, прикрутил два болта, вставил три разъема и печатаешь.
Теперь, постараюсь кратко, но в красках и с иллюстрациями, показать тот путь, который я прошел при сборке набора с верхней фотографии.
1. После тщательного пересчета и проверки всех компонентов, можно приступать к сборке рамы
Сначала - надо отсортировать все профили по размерами и начать собирать по сборочному мануалу.
В профилях сделаны отверстия, углы стягиваются друг к другу с помощью T-NUT. В мануале подробно описано, какую гайку и куда вставлять. Ошибок в нем не найдено, так что если что-то не сходится или есть сомнения - лучше сразу найти первопричину, чем разбирать все и начинать заново!
На сборку рамы у меня ушло несколько часов: тщательно выравнивал профили между собой, "ловил" плоскость, прямые углы и прочие мелочи. Собирайте все надежно и вдумчиво.
После сборки рамы, предстоит долгий и кропотливый процесс вставки втулок в пластиковые детали.
Для печати деталей подвижной балки и экструдера я использовал пластик Filamentarno Aerotex (он легче других материалов и обладает хорошей термостойкостью), для всех малоподвижных деталей внутри камеры - использовал Filamentarno Total GF-10, а для ног и боковых юбок взял обычный PETg.
2. Сборка пластиковых деталей
Если вы их еще не напечатали, то приготовьтесь - их много, все разные, печатаются в разном количестве, каике-то штучно, какие-то по 2, а какие-то по 3 или 8 штук. В этом месте нужно проявить внимательность и собранность, тщательно подготовить задания на печать. Настройки слайсера для печати - так же в мануале. Все печатается без поддержек, заполнение 40%, gyroid.
Все пластиковые детали собираются с помощью гаек-вставок, которые садятся в пластик при температуре около 200 градусов. Очень удобно использовать паяльник с поддержкой заданной температуры и жалом в форме иглы или конуса.
Типичная картина у вас на столе, на протяжении месяца, будет выглядеть примерно так:
Так что можете заранее расстаться с частью балкона, квартиры или другой полезной площадью на все время сборки.
3. Сборка ног \ моторов подъема гентри
Гений инженерной мысли придумал разместить моторы со шкивами в ногах, а раму с экструдером поднимать на длинных ремнях, проходящих через весь принтер "от крыши до подвала". Сложностей тут нет, главное - все протянуть, не забыть спейсеры в 1мм на валах. Подход к сборке всего принтера такой: затягиваем все плотно, но без фанатизма.
Примерно в таком виде я наблюдал принтер на протяжении месяца. Работал, в основном, по вечерам и по выходным. Каждый день по 3-4 часа.
4. Линейные направляющие
В этом наборе используется несколько видов направляющих: 4 штуки для перемещения гентри вверх-вниз, две штуки - для перемещения балки с хотендом и одна штука - для перемещения каретки хотэнда. Все направляющие, кроме одной - MGN9. Для каретки - MGN12.
Не разбираюсь в китайских брендах линейных направляющих, но меня качество более чем устроило. Работают плавно и без люфтов.
Мне стало интересно, почему же для хотенда выбрали другую направляющю? Неужели 9мм было недостаточно? Оказалось, здесь проблема носит несколько иной характер: направляющая крепится к алюминиевому профилю на болты, а у стали и алюминия разные коэффициенты теплового расширения! В результате пара профиль+направляющая работает как биметаллическая пластинка и изгибается от нагрева камеры даже на 30 градусов! Энтузиасты посчитали, что у 350мм версии Voron, стандартная MGN9 рельса гнется в пределах 0.2мм, а MGN12 - меньше, чем 0.05мм. Поэтому, в новых ревизиях используется MGN12 для хотенда. Для рельс портала же прикручивают стальные пластины с противоположной стороны, таким образом, эффект биметалла компенсируется "триметаллом".
Подробно об этом эффекте можно почитать на Github extrusion_backers.
В моем наборе таких пластин не было, поэтому рассказать на своем примере об их влиянии я не могу. Но, я не смог зафиксировать разницу более, чем в 0.05мм между краем и центром, как на прогретом, так и на холодном принтере, измерения проводились микрометром.
Важно: направляющие надо смазывать перед установкой. Я использовал обычный шприц, набитый смазкой. В мануале на этом пункте отдельно заостряется внимание.
5. Натяжители ремня оси Z
Деталь очень простая, их всего четыре штуки. Комплектные шкивы хорошего качества, биений и люфтов не обнаружено. Всего таких натяжителей 4 штуки, устанавливаются вверху в каждом углу рамы.
Один важный нюанс - болт, фиксирующий шкив, лучше устанавливать шляпками внутрь камеры, чтобы его можно было достать без снятия успокоителя. Это может потребоваться для установки, например, светодиодной ленты или в случае замены ремня. После сборки, боковые панели будут мешать вам достать этот болт.
Общий вид:
6. Установка стола и нагревателя
Стол у этой модели закреплен неподвижно и это правильно. Массивная алюминиевая пластина, отфрезерованная на заводе с допуском в 0.01мм - это не шутки. Толщина пластины - 10мм, размеры 355х355мм.
В упаковке в месте с пластиной был лист с китайским ОТК, в котором говорится что пластина ровная, в пределах 0.01мм.
Для нагрева массивной пластины алюминия используется 650w грелка, размером почти во весь стол, клеится на 3М скотч.
Перед установкой грелки, пластину надо зачистить наждачкой или жесткой губкой, обезжирить спиртом.
После тщательной зачистки (это делается в нитриловых перчатках), снимается защитное покрытие с грелки, ставится под пресс. Все стыки я промазал автомобильным герметиком, с термостойкостью до 340 градусов.
После высыхания (я выдержал сутки), точно также приклеивается магнитная сторона. Есть отдельное описание этого процесса в руководстве. Если кратко - полностью защитную пленку не убираем, вытягиваем ее постепенно, по мере приклеивания магнитного
После, в магнитном слое делаем отверстия под болты и прикручиваем к раме, лист PEI магнитится намертво!
7. Сборка гентри, осей Х и Y
Пожалуй, самое кропотливое, после электрики - это сборка гентри (Портала). Нужно все делать точно, четко, правильно прокладывать ремни. Опять же - вдумчиво, внимательно и основательно.
Сначала - линейные направляющие оси Y. Смазка, установка по шаблону, равномерная протяжка от центра к краям. Болты крутятся через один.
На фото - шаблон для установки направляющих:
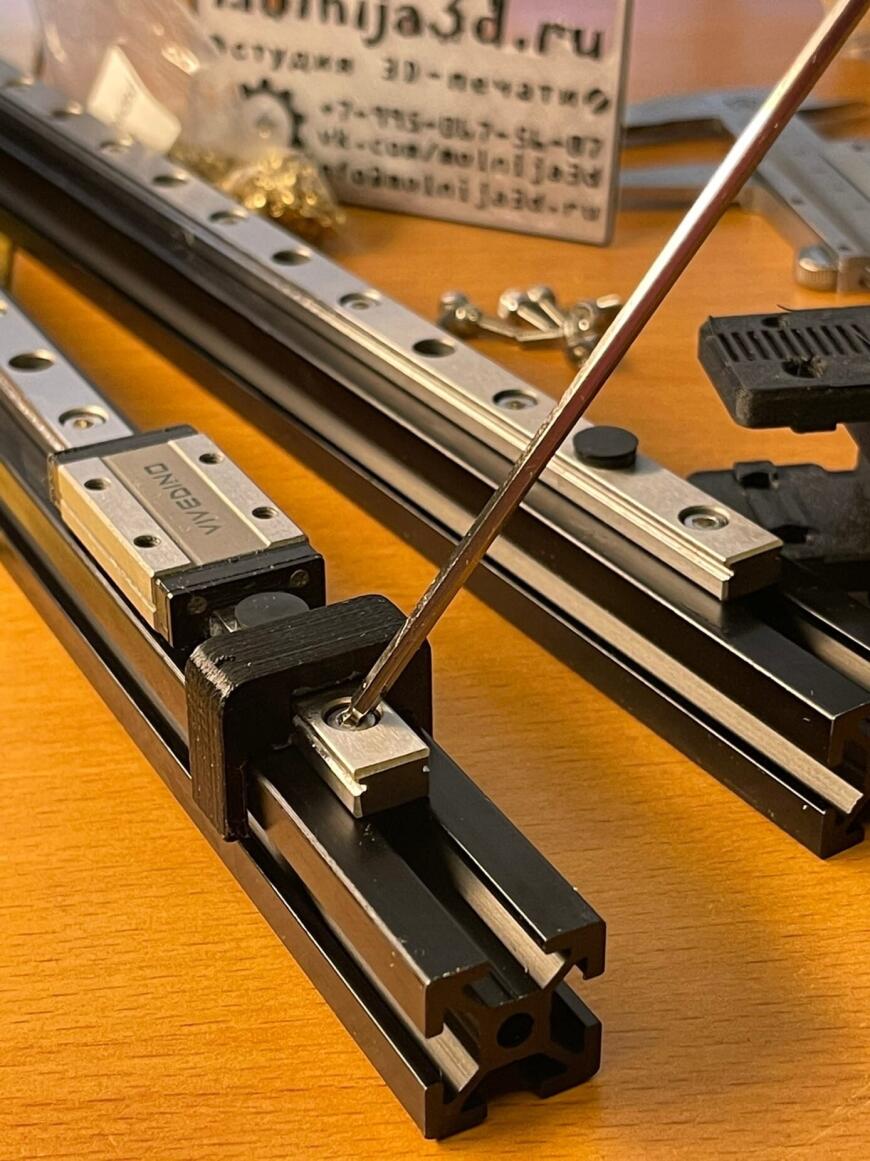
Далее, идет процесс сборки всех пластиковых частей. моторов, фиксаторов и корпусов:
Моторы и натяжители А и Б выглядят одинаково, но печатаются в зеркальном исполнении. Очень важно правильно установить все спейсеры, сориентировать шкивы в нужном направлении. Болтовые соединения затягиваются с разумным усилием. Плотно, но без фанатизма.
Штангенциркуль, паяльник и отвертка с шестигранником будет сопутствовать вам во время всего процесса сборки.
Отдельное внимание скажу про ремни, их много видов - маленькие петли для оси Z, ремни средней длины (4шт) для оси Z и двухметровые (2шт) для оси X и Y. Подробно про длины и регулировку расписано в мануале. Этот момент требует особого внимания. Случайно, я чуть не обрезал длинный ремень, так как сначала не нашел короткий, но, еще раз все перепроверил и все встало на свои места.
Еще один важный момент - ремни устанавливаются почти в слепую - путь к роликам сложный и закрыт крышками. Нужно тщательно проверять, не пропустили ли вы ремень мимо ролика и свободно ли он ходит. Это, оказывается, не так просто понять. После сборки принтера, я долго искал проблему в конфигурации клиппера и не мог понять, почему же каретка все время едет в неверном направлении, пока не понял что дело не в моторах и их конфигурации, а в том что один ремень движется немного туже, чем другой. Дело было в ремне, пропущенном через пластиковое ухо мимо ролика.
Один из признаков - движение второго мотора в неверном направлении, когда каретка двигается вручную.
Ремни подрезаются на этапе установки каретки. Важное правило - ДЛИНА РЕМНЕЙ для А и B - ОДИНАКОВАЯ. Установили ремень А. Отрегулировали. Сняли А, обрезали по нему ремень B, установили оба ремня обратно. Провисание компенсируется натяжителями с каждой из сторон портала. Расположены они очень удобно, можно регулировать даже во время работы принтера.
На фото выше- каретка с установленным индукционным датчиком расстояния. Он используется для выравнивания портала относительно стала, допуск - 0.0075мм.
Важный момент. Настоятельно НЕ РЕКОМЕНДУЮ ставить штатные механические концевики осей X и Y. Лучше поставьте датчики холла, их показания стабильны. Причина проста - пружинный контакт на штатных концевиках обладает дрейфом плюс-минус 2мм, вследствие чего, координаты ноля все время плавают из стороны в сторону, впоследствии, это может привести к промаху мимо концевика оси Z, ноль откалибруется с ошибкой и сопло будет с самурайским упорством протирать стол. Что в моем случае и произошло.
На фото - старые механические концевики и новые - с датчиком холла.
Для концевиков с датчиком холла требуется печатать деталей с пазами под магниты (одна сторона каретки экструдера и держатель портала). Рекомендую сразу же печатать версии с отверстиями под магниты. Заглушку вставить можно, но пересобирать все заново из-за такой мелочи - затея длиной в день работы.
8. Сборка экструдера
Экструдер собирается из стандартных компонентов к BMG экструдеру. Все моторы - Moons с повышенным классом термостойкости (до 130 градусов).
Набор компонентов для экструдера
Ничего сверхъестественного тут нет. Все просто и лаконично, но, что бы вставить правильно прижимную лапку, мне пришлось постараться.
В качестве хотенда - Triangle Lab Dragon HF v2.0. На мой взгляд, одно из лучших решений на рынке. Обладает невероятной производительностью. Цельнометаллический термобарьер с расширенной зоной нагрева и медный нагревательный блок позволяют печатать на больших потоках и при высоких температурах. В качестве термистора взял T-D500 (до 450с), а в качестве нагревателя - 24v 50w, все от тех же треугольников.
С этим хотендом, мне удалось достичь реального потока без пропусков и недоэкструзиии около 65-70мм^3/c (сопло 0.6мм, ширина 0.8, высота 0.3, скорость по логам клиппера - 300-400мм\с), при больших значениях все упирается в охлаждение, модели просто стекают, не успевая остывать. Причем, на потоках выше примерно 50мм3/c - чувствуется нехватка 40w нагревателя (особенно на PETg) и температура хотенда падает, пока не снизишь скорость печати, когда же установлен 50w нагреватель, такой проблемы не замечено.
Решение по обдуву оригинальное и эффективное. Но сейчас, пройдя весь путь от начала и до конца, с уверенностью 100% скажу: если используете отличный от E3D V6 хотенд - печатайте AB-BN мод! Штатного обдува не хватает для Dragon Hotend и вы будете постоянно сталкиваться с пробками в термобарьере.
Сейчас, я бы уже стал делать экструдер stealth burner вместо штатного afterburner. Там много улучшений. Но, для него нужно покупать мотор NEMA14, NEOPIXEL и прокладывать еще один 3-ех проводный кабель.
9. Сборка боковых юбок
Пожалуй, это самое простое в сборке принтера. Главное - распечатать все в нужном количестве. На юбки у меня ушло около килограмма пластика! Опять же, все собирается на гайках-вставках.
Левая сторона от правой отличается наличием\отсутствием вентиляторов, поэтому, посадочные площадки разные.
10. Подключение электроники и электрика
Китайцы кладут в набор комплект предварительно обжатых проводов нужной длины и еще несколько запасных пакетов с разъемами, видимо, на всякий случай. Все в нужном количестве, провода очень хорошего качества, сечения выбраны с запасом.
Электрика монтируется на WAGO, все удобно и
Первый шаг - размещение компонентов на DIN-рейке. Для крепления всего, кроме твердотельного реле, используются печатные детали. Мной был приобретен одноплатник Orange Pi PC Plus, проектом же не предусмотрены крепления для него, поэтому оно было смоделировано и распечатано собственноручно.
При размещении и разведении питания всех модулей придерживался такой логики: максимально отдалить слаботочные цепи от 220в и минимизировать количество точек пересечений слаботочными цепями силовые линии. Параллельно с 220в слаботочку пускать тоже не рекомендуется.
Разводка силовой части - на фото выше.
Прокладка слаботочных цепей... Делать нужно внимательно и тщательно. Все провода промаркированы, ошибиться сложно. В мануале подробная инструкция о том как и куда подключать.
Все провода упаковываются в гибкие кабель каналы, всего в наборе три штуки: два узких для оси Х и Y и один широкий для оси Z.
Монтаж проводов и кабелей у меня занял два вечера. Делал неспешно, но аккуратно.
Проводов очень много! Запутаться легко. Сначала, я смонтировал кабель-каналы, потом укладывал в них провода и сразу же подключал к платам управления. Перепроверял и только тогда приступал к следующей группе проводов. Кабели должны лежать свободно, без натяга и сильных перегибов. Начинал монтировать от экструдера - от крышки, закрывающей все разъемы.
Примерно так, это выглядело до укладки проводов:
Вид после укладки проводов. Фиксируются с помощью стяжек прямо к стеклянной панели. Стяжки приклеиваются на двусторонний скотч через специальные платформы.
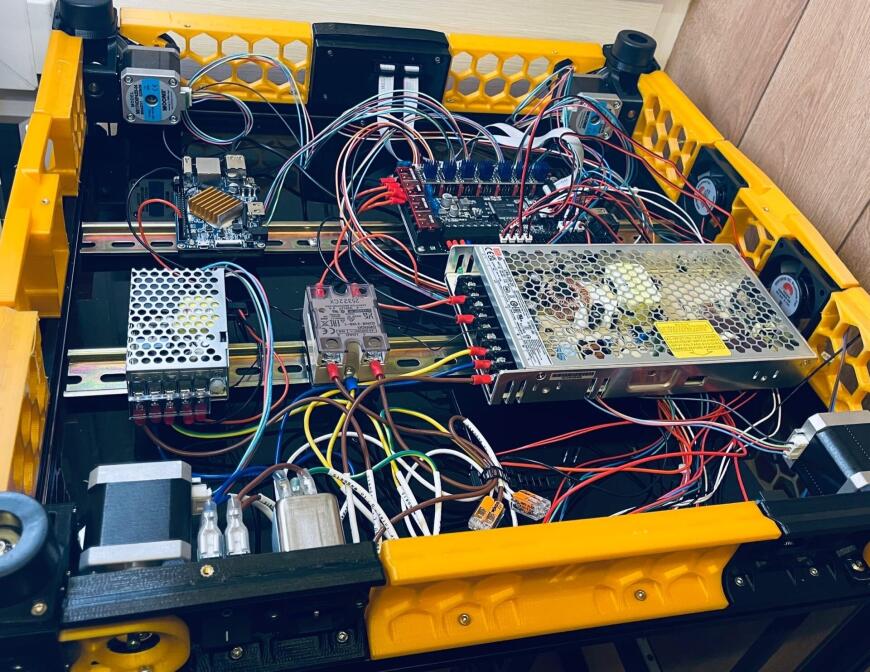
По-моему, получилось вполне аккуратно и даже красиво:
Так выглядит блок электроники, если заглянуть через решетку охлаждения. Космически и завораживает:
11. Установка и настройка ПО
После всех подключений, приступил к настройке и установке клиппер. Если буду описывать здесь весь процесс настройки - то получится материал больше, чем вся статья. Поэтому лишь опишу самые важные, на мой взгляд рекомендации:
1) Лучшая операционная система для Orange Pi - Armbian. Не пробуйте другие, не проходите мой путь проб и ошибок. Это единственная ОС, на текущий момент, в которой все работает из коробки, нужно лишь настроить сеть, установить нужные пакеты, разграничить права пользователей и т.д. С остальными ОС очень много непонятных багов и лулзов. Они решаемы, но время, которое вы на это потратите - бесценно. Мне потребовалось 4 дня чтобы прийти к Armbian.
2) Не ставьте Octoprint. Используйте Fluidd или Mainsail. Минимум проблем - максимум стабильности и быстродействия, цена этому - меньший функционал.
3) Сразу же настраивайте Orange PI как Secondary MCU. В этом пункте есть сложность: то, что написано в руководстве - не работает для Orange PI. Но все гуглится по запросу "Orange Pi enable SPI". Придется поработать ручками. Мне помогло добавление этих строк в /boot/armbianEnv.txt:
sudo nano /boot/armbianEnv.txt
overlays=spi-spidev
param_spidev_spi_bus=0
param_spidev_spi_cs=0cs=0
param_spidev_max_freq=1000000
Включение SPI через armbian-config, в моем случае, не сработало - отдельно не включался pin CS0, необходимый для работы SPI. Остальные работы как по инструкции с сайта klipper.org
4) Для настройки всего ПО и железа, вам придется основательно зарыться в инструкции с этих сайтов:
- docs.mainsail.xyz (если вы выбрали mainsail)
- docs.fluidd.xyz (если вы выбрали fluidd)
- Print-Tuning-Guide (много советов, как по настройке железа, так и софта)
- VoronUsers (настройки, конфигурации, моды, руководства по настройке, опыт и т.д.)
5) Рекомендую подключать ethernet розетку сзади принтера (идет в комплекте). Просто удобно. Принтер переезжал с места на место и для настройки Wi-Fi пришлось бы каждый раз разбирать и подключать кабель прямо в Orange-Pi.
Hello world от ворона выглядит так:
Первое удачное включение - на фото выше.
Принтер почти собран - остались лишь боковые стенки. Но, уже можно отправить пробник на печать. Конечно, этой печати предшествовали и другие настройки. типа калибровки оси Z, датчика приближения, высоты ENDSTOP, силы прижима, выравнивания углов портала и т.д. - все это детально описано в руководствах, при выполнении обязательно включать здравый смысл. В моем случае, обошлось без сюрпризов (кроме неправильной установки ремней) и все шаги были выполнены с первого раза.
Первая печать - рыбка. Получилось с первого раза.
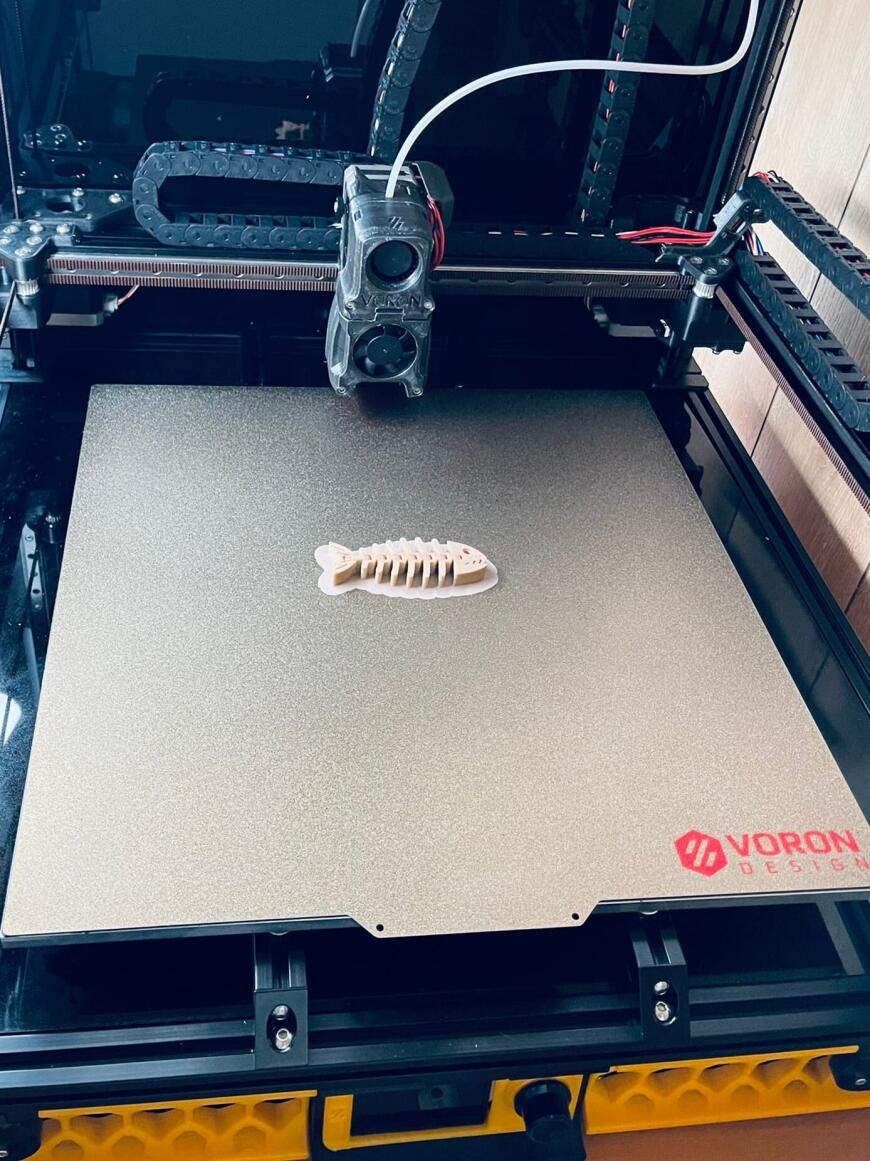
12 Установка боковых крышек
Перед установкой крышек я еще раз проверил затяжку всех доступных болтов, напечатал еще несколько моделей и приступил к сборке. Это простой процесс.
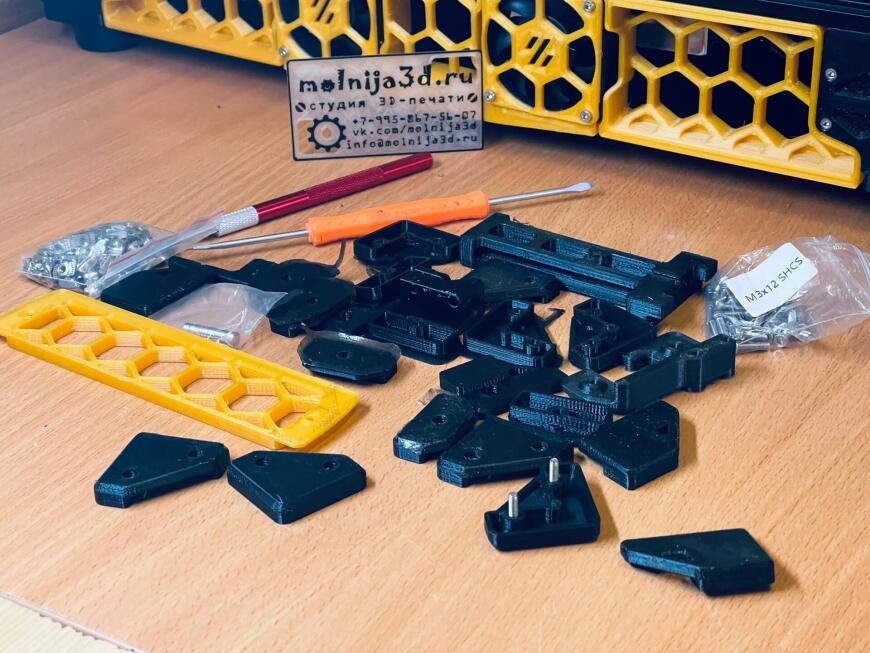
Так выглядит полностью собранный принтер:
13. Пользовательские моды. Их установка и настройка носит рекомендательный характер, про самые важные, на мой взгляд, читайте ниже.
13.1 Установка подсветки
В качестве подсветки я использовал две светодиодных ленты по бокам. Количество диодов 60шт на 1 метр. Лучший вариант мода для подсветки, на мой взгляд - eddie LED_Bar_Clip
Провода прокладываются прямо в алюминиевом профиле, по углам закрываются крышками corner_cable_hide, а в отсек электроники попадают через заглушки моторов оси Z. Их я не стал перепечатывать, просто сделал аккуратные прорези ножом. Ленты подключал в свободные порты для нагревателей, просто потому, что провода можно вставить прямо в колодку на плате и протянуть болтами.
13.2 Настройка Input Shaping и компенсации резонанса
Для начала, простыми словами опишу что это такое. Принтер, во время печати передает вибрации на корпус, которые с некоторой задержкой передаются обратно в систему. На определенных частотах возникает резонанс и этот эффект усиливается. Проявляется как дефекты печати в виде ЭХО на моделях. Сенсор ADXL 345 устанавливается на печатную голову (только на время тестирования), специальными скриптами на моторы подаются управляющие сигналы, которые заставляют их вибрировать на определенных частотах, датчик же фиксирует ускорения и на основании данных строится кривая резонанса. После чего, выбираются частоты и оптимальный алгоритм компенсации резонанса. Детально и в картинках про это написано на сайте, глубже описывать не вижу смысла.
Датчик работает по SPI, если вы его сразу не включили на Orange Pi и не переконфигурировали Klipper на работу с Secondary MCU - то это придется сделать сейчас.
Все подключения - по мануалу на одноплатник. Там расписано какие пины и за что отвечают. В инструкции на сайте клиппер все хорошо расписано. В моем случае (Orange Pi PC Plus) это выглядело вот так:
Заодно, я проложил термодатчик камеры, что бы сделать активную термокамеру:
Разъем для датчика монтируется прямо в вентиляционную решетку. Есть несколько готовых модов, нужно лишь распечатать и собрать:
1) microfit_2x3_skirt_connector_adxl
Так выглядит график резонанса и рекомендации по его компенсации:
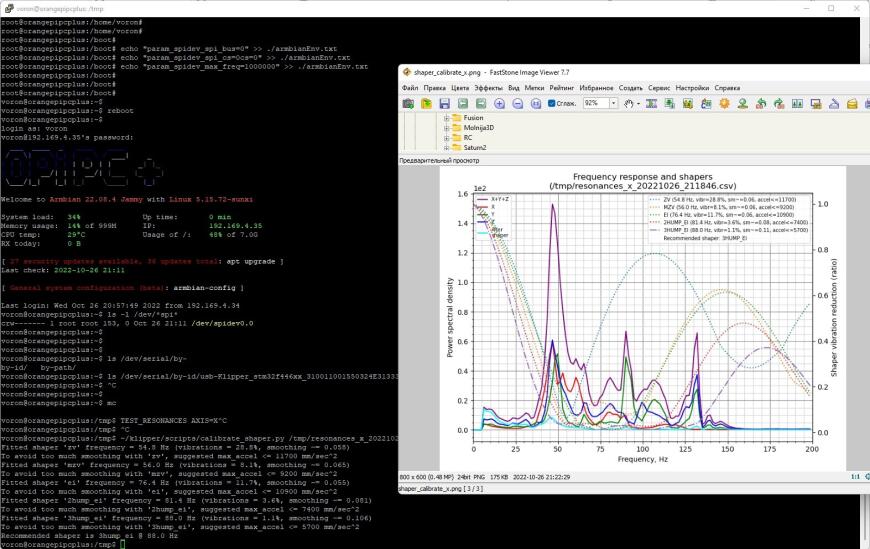
Эффект от компенсации резонанса существенный. Эхо исчезло, углы стали почти идеальными. Но, у всего есть цена - на таких моделях, как шестеренки, зубья могут быть сглажены шейпером. Поэтому, лучше ограничивать степень компенсации. Об этом так же подробно расписано в руководстве по настройке Measuring_Resonances.
13.2 Датчик температуры камеры
Много думал про оптимальное место для размещения датчика, какого-то стандартного и проверенного решения не нашел, поэтому решил разместить рядом со светодиодной лентой, так удобнее всего. Провода проложены все так же прямо внутри алюминиевого профиля. В качестве датчика - обычный NTC 100 3950.
Для фиксации проводов использовал следующий мод: corner_cable_hide
13.3. Установка веб камеры
В качестве камеры, выбор пал на OV 9726. Угол обзора в 50 градусов почти перекрывает всю область печати. Более чем достаточно для контроля процесса печати. Одна сложность - нет модели для крепления камеры, нарисовал в CAD за пару минут.
На фото ниже, камера на кронштейне. Углы вымеряны так, чтобы в камеру попала вся область печати, по возможности.
Вид со стороны стола на камеру:
Дельных инструкций по настройке камеры, я не нашел, пришлось изучать множество источников. Основные проблемы, с которыми я столкнулся - это косяки при установке и конфигурировании MJPG-streamer, установке его как системной службы и подборке подходящего кодека для камеры и web интерфейса. Все эти проблемы решается с помощью поисковика. Ссылок не привожу, так как их нет и они будут отличаться в зависимости от вашей конфигурации.
13.4 Установка "ведра" и "щетки"
Этот мод позволяет производить авто-очистку сопла перед печатью, после паузы или смены пластика.
Сложность возникла только одна - макросы. Готовые решения, которые есть - не работают, так как их версии устарели и поменялся синтаксис. К тому же, написаны с косяками. Поэтому, ниже привожу свои макросы, которые работают на 350мм версии на текущий момент времени (11.11.22):
[gcode_macro G32]
gcode:
SAVE_GCODE_STATE NAME=STATE_G32
G90
G28
QUAD_GANTRY_LEVEL
######################## purge nozzle
G1 Z5 F5000 ; move nozzle away from bed
PURGE_BUCKET
########################
G28
G0 X175 Y175 Z10 F5000
RESTORE_GCODE_STATE NAME=STATE_G32
[gcode_macro PRINT_START]
gcode:
G32 ; home all axes
G90 ; absolute positioning
###############################################
[gcode_macro PURGE_BUCKET]
gcode:
SAVE_GCODE_STATE NAME=PURGE
G90 ; absolute
G0 X65 Y360 Z2 ; go to purge bucket
M83
G1 E10 F500 ; purge some filament into bucket
G0 X130 Y360 F750 ; move across purge brush
G1 E-2 F500 ; Retract a little
G0 X65 Y360 Z2 ; go to purge bucket
G1 Z5 F5000 ; Raise and return
RESTORE_GCODE_STATE NAME=PURGE
14. Что не вошло в обзор
В этот обзор не вошло несколько полезных модификаций, по одной простой причине: про них я узнал через несколько месяцев, после того, как закончил работу над принтером, поэтому запчасти в пути. Это:
1) Циркуляция для активной термокамеры. Работает на четырех вентиляторах 5015, стандартный функционал предусматривает несколько режимов: выключена, минимальный обдув, средний обдув, максимальная мощность.
2) Stealth Burner - более свежая модель экструдера, в которой улучшены такие моменты, как работа с гибкими материалами, обдув, охлаждение хотендов, отличных от e3dv6, изменено передаточное соотношение в сторону большего момента на шестернях. Кроме того, добавлены NEOPIXEL для отражения статуса работы принтера и предусмотрено штатное место для установки ADXL 345 во время калибровки.
Подведение итогов
На сборку, отладку и настройку этого принтера, у меня ушел месяц неспешной и вдумчивой работы. Стоило ли оно того? На мой взгляд - однозначно. Самый важный момент - это опыт, полученный во время работы над этим проектом. Хочешь или нет - придется глубоко разобраться с линуксом, тонкостями работы электроники и механики, параметрами и на стройками прошивки, режимами печати. Впечатляет и то, что все пластиковые детали печатаются без поддержек. У команды VorodDesign, определенно, есть чему поучиться. Этот опыт, легко перенести на другие проекты и заказы.
Набор деталей от Formobot, однозначно, стоит своих денег. В случае правильно сборки и настройки, качество печати - на высоте. Слои укладывает ровно, геометрические искажения минимальны.
Возможность удаленного управления и контроля статуса через камеру, невероятная объемная скорость печати, стол размером 350 на 350см, все это делает Voron 2.4R2 отличным вариантом для бизнеса.
Внешний вид завораживает, равно как и процесс калибровки углов (quad leveling), похожий на танец экструдера над столом, "уау-эффект" обеспечен.
Заключение
Этот обзор, я начал с упоминания пути джедая, поэтому в этом стиле и будет заключение. Построить свой собственный Voron 2.4 R2 и пройти "путь" - вариант не для всех. Это требует навыков, это дорого и это долго. Сумма средств, затраченных на завершение этого проекта, в пересчете на потраченное личное время и все компоненты приближается к 150 000 - 200 000т.р., в зависимости от того, где будете покупать детали. Стоит оно того, или нет? Решать вам, но, я рекомендую пройти этот путь, как минимум один раз. каждому, кто занимается 3Д-печатью, не важно, хобби это или источник заработка.
Еще больше интересных статей
UniFormation GK3 Pro — профессиональный 3D‑принтер нового поколения
Подпишитесь на автора
Подпишитесь на автора, если вам нравятся его публикации. Тогда вы будете получать уведомления о его новых статьях.
Отписаться от уведомлений вы всегда сможете в профиле автора.
Двойной Удар Радуги! Тестируем 2 Огненных Новинки SILK PLA от Rittsun: Адреналин vs Кислотный Трип!
Подпишитесь на автора
Подпишитесь на автора, если вам нравятся его публикации. Тогда вы будете получать уведомления о его новых статьях.
Отписаться от уведомлений вы всегда сможете в профиле автора.
На что способен лазерный гравер мощностью 2500mW
Подпишитесь на автора
Подпишитесь на автора, если вам нравятся его публикации. Тогда вы будете получать уведомления о его новых статьях.
Отписаться от уведомлений вы всегда сможете в профиле автора.
Комментарии и вопросы
Игорь Иванович, перелогинтесь....
Сделали два крюка - ПЛА держит...
Что именно вы подразумеваете п...
Скажите пожалуйста кто знает,к...
Всем привет, недавно купил себ...
Уважаемые коллеги! Работаю в б...
Старый столик крепился винтами...