Домашнее производство прутка или Экономика должна быть экономной
Одним из новейших развитий устройств для 3D-печати стало появление экструдеров. Нет, речь пойдет не о печатающих головках FDM-принтеров, хотя это тоже экструдеры, а о портативных настольных устройствах для домашнего производства пластикового прутка.
Что, вообще, такое экструдер? Это устройство для формирования изделий путем плавки или разжижения расходного материала и выдавливания массы через отверстие определенной формы. Фактически, обычная мясорубка суть своего рода экструдер.
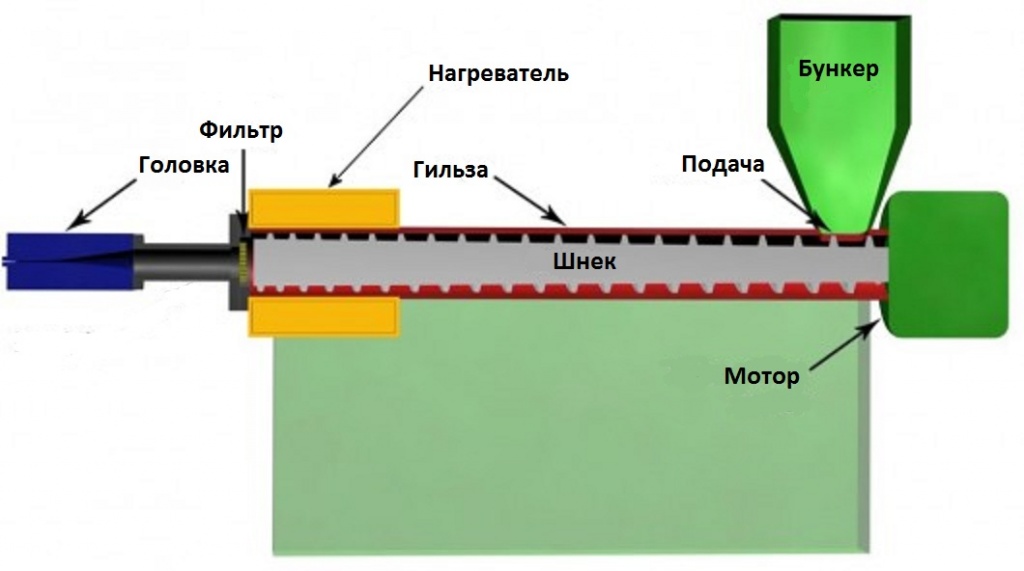
Именно подобные «мясорубки» и используются для промышленного производства прутка для 3D-печати. Причем, конструкция таких устройств предельно проста: гранулы пластика засыпаются в бункер и с помощью шнека (он же «Архимедов винт») перемещаются внутри разогретой трубки, или «гильзы». К концу недолгого путешествия пластик нагревается почти до точки плавления и выдавливается шнеком сквозь круглое отверстие в «головке», образуя нить. Затем производится охлаждение нити и намотка на бобину. Казалось бы, ничего сложного. Так почему бы не заняться производством нити в домашних условиях?
Это вполне возможно. Зачем? Хотя бы из-за того, что гранулы того же ABS-пластика стоят намного дешевле, чем готовый пруток аналогичного веса. Насколько? Сравните сами: тысяча-полторы рублей за готовую катушку с килограммом нити или 50-70 рублей за килограмм пластиковых гранул.
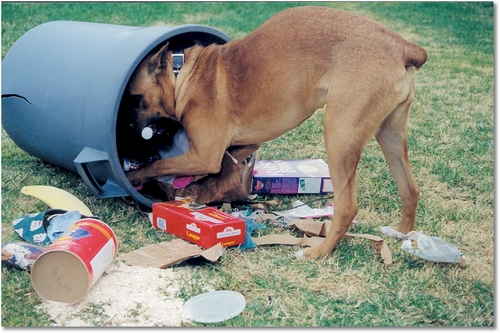
Кроме того, у вас будет возможность контролировать процесс. Мало ли кто и что подмешивает в расходные материалы ради снижения себестоимости? И наконец, у вас будет возможность экспериментировать с различными материалами, считающимися «экзотичными» в мире 3D-печати, но в реальности зачастую валяющимися прямо под ногами. Взять, хотя бы, тот же ПЭТ, из которого изготавливаются чуть ли не все пластиковые бутылки для напитков. Это и бесплатный расходный материал, и способ улучшить экологию.
Изготовить экструдер можно из подручных материалов, но рост популярности подобных устройств привел и к появлению коммерческих моделей. Сегодня мы взглянем на наиболее известные решения, а подробности постройки экструдера своими руками мы позже опубликуем в нашей Вики.
Filabot
Самая известная марка на рынке, представленная линейкой экструдеров и дробилкой для пластика. О дробилке чуть позже.
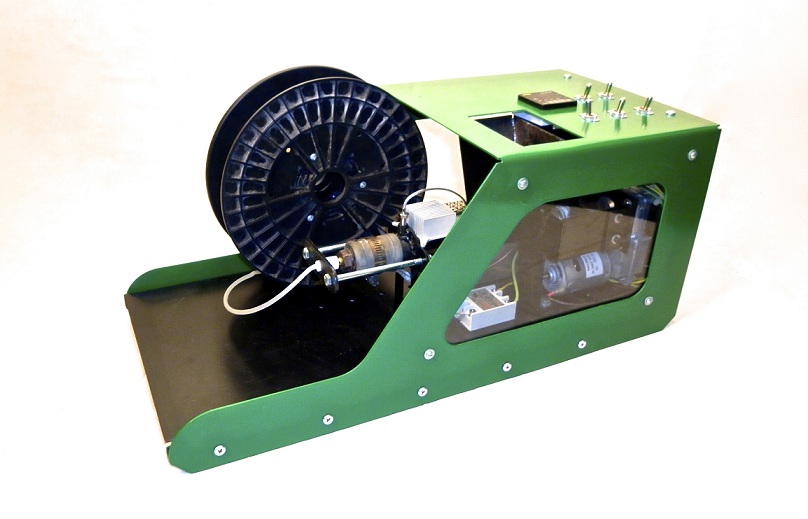
Первой моделью компании стал экструдер Filabot Original – достаточно симпатичное устройство размером с системный блок компьютера. Согласно заявлениям разработчиков, устройство способно производить нить из ABS, PLA и HIPS, да еще и c возможностью добавки углеволокна. Кроме того, возможна добавка красителей. Производительность устройства высока, достигая 1кг пластика за пять часов работы или около 45 метров прутка в час. Другими словами, эта машинка может вырабатывать пруток быстрее, чем среднестатистический FDM-принтер сможет его расходовать.
И здесь возникает одна небольшая проблема, хоть и не критичная: при такой скорости экструзии было бы неплохо оснастить устройство вентилятором для охлаждения пластика на выходе, иначе возможно растяжение нити под собственным весом или слипание. К сожалению, разработчики не озаботились этой проблемой, видимо считая, что экструзия будет производиться со стола на пол, с достаточным временем для охлаждения перед сматыванием…
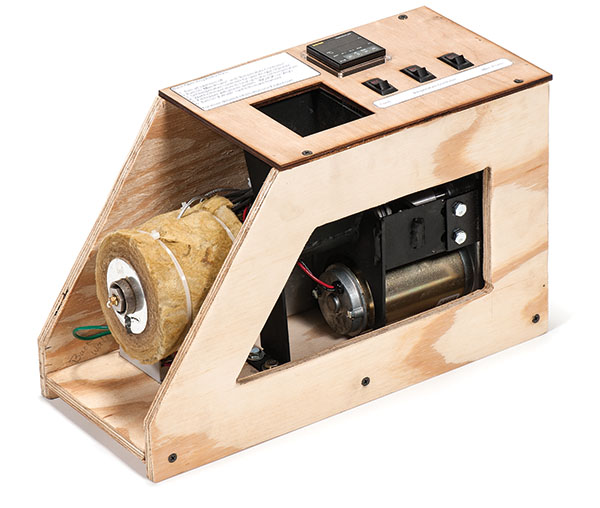
Более серьезной проблемой представляется стоимость экструдера – ни много, ни мало $900. В забавной попытке снизить стоимость устройства компания решила придержаться своей маркетинговой стратегии и предложила Filabot Wee. Эта модель мало чем отличается от оригинала, если не считать деревянного корпуса, но стоит уже $750. Наконец, есть возможность приобрести Filabot Wee в виде комплекта для сборки за $650.
Filastruder
Filastruder был разработан парой помешанных на филаменте (см. видео) умельцов-студентов по имени Тим Элморе и Аллен Хэйнс из Университета Флориды в ходе закрытого проекта, затем успешно протестирован среди не менее помешанных 3D-мейкеров и, наконец, предложен на Kickstarter в уже готовом виде в качестве дешевой альтернативы экструдерам Filabot. Стоимость устройства составляет всего $300.
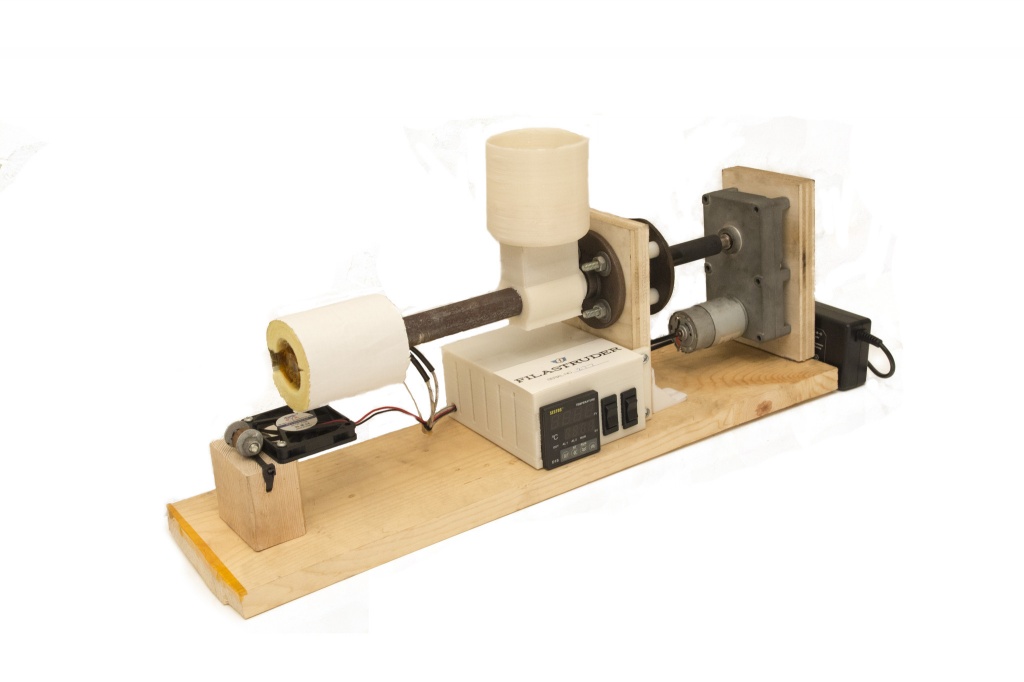
Производительность Filastruder в сравнении с Filabot обратно пропорциональна цене, достигая порядка 1кг пластика за 12 часов работы. Но как мы уже отметили, темп работы Filabot просто избыточен для домашней печати. Для нужд энтузиаста-одиночки производительности Filastruder вполне хватит, а более скромный ценник станет несомненным преимуществом. Filabot же лучше подходит для использования группами мейкеров, либо в качестве источника дохода. Почему бы и нет? Четыре-пять килограммов нити в день могут преобразиться в неплохую сумму, если есть покупатели.
Lyman extruder
С чего, собственно, все и началось. Скромный 83-летний пенсионер из штата Вашингтон (что, кстати, на противоположном побережье от столицы США) решил показать молодежи «что к чему». И таки преуспел! Вооружившись лобзиком, дрелью, отверткой и талантом, мистер Хью Лайман соорудил устройство для экструзии прутка. Ну, хорошо: может он и не был зачинщиком, ибо идея витала в воздухе достаточно долгое время, но именно Хью разработал простую, годную установку и выложил чертежи в открытый доступ, что уже делает его героем среди 3D-мейкеров.
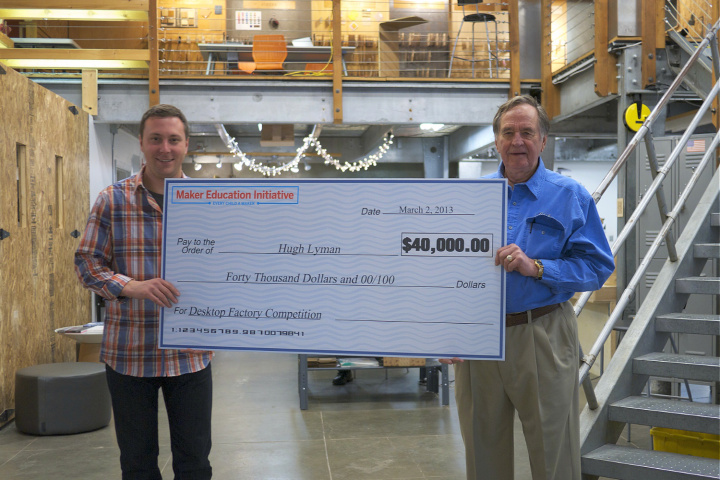
Кстати, этот уже не молодой человек имеет вполне интересный, хоть и малоизвестный список заслуг. К примеру, в 70-х годах он возглавлял компанию Ly Line, которая пыталась продвинуть на рынок портативные компьютеры лет этак за восемь до появления первого серийного «макинтоша». Правда, весило сие «портативное» устройство скромные 25кг... Но ведь идея была правильной? Вот и в этот раз Хью Лайман, уже на пенсии, не оплошал.
Как оказалось, Хью заинтересовался 3D-печатью. Он не считает себя полноценным инженером – диплом он так и не защитил, несмотря на университетское образование. С другой стороны, талант превыше бюрократии. Побаловавшись с 3D-принтерами, Хью пришел к выводу, что технология приятна, а вот ценник в $30-40 за килограмм прутка несколько раздражителен. Услышав о конкурсе Desktop Factory Competition, то есть «конкурсе самодельных настольных фабрик», Лайман решил тряхнуть стариной.
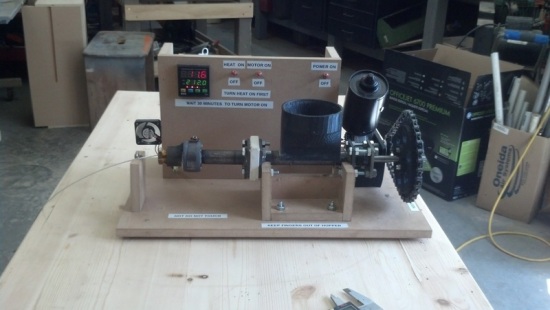
Условием соревнования было создание генерирующего устройства из общедоступных компонентов с общей стоимостью менее $250. Свою первую попытку Лайман с блеском провалил по одной простой причине: он не учел стоимость собственноручно изготовленных компонентов, а тем самым нарушил условия конкурса, превысив условную стоимость. После быстрой доработки дизайна на свет явилась вторая версия экструдера Лаймана. Результат? Безоговорочная победа. Еще бы: даже с учетом затрат на электроэнергию стоимость самодельного прутка, произведенного из гранул, ниже стоимости «фирменного» продукта в разы. А уж если использовать «подножный» материал… Кстати, о мусоре:
Filabot Reclaimer
Основным ограничением экструдеров является использование гранул для производства прутка. Ни Filabot, ни Filastruder, ни экструдер Лаймана не способны «переварить» крупные куски пластика. Таковы особенности и ограничения дизайна. А ведь основной потенциал домашних экструдеров именно в переработке пластиковых отходов: бутылок, упаковки и просто неудачных моделей или отходов 3D-печати – рафтов и опор.
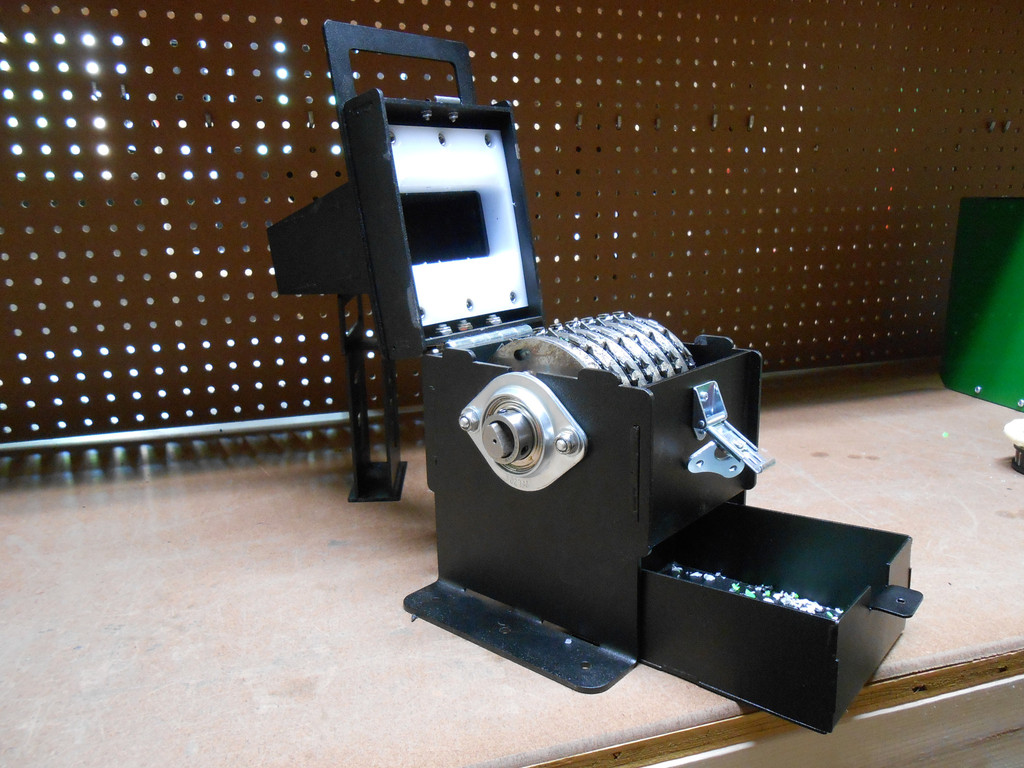
К счастью, эта проблема решается достаточно просто: разработчики Filabot уже предлагают дробилку для пластика под названием Filabot Reclaimer. Это устройство отличается исключительной экологичностью при мощности в одну человеческую силу. Другими словами, это шредер с ручным приводом. Устройство дробит пластик в частицы размером менее 5мм, превращая пластиковые отходы в удобоперевариваемое сырье для экструдеров. Цена вопроса: $440. Да, недешево. Зато сырье бесплатное. Разработчики указывают на возможность переработки ABS, PLA и HIPS.
В общем и целом, идея домашних устройств для производства прутка, включая переработку пластиковых отходов, достаточно нова. Конечно же, появления подобных устройств стоило ожидать – это вполне логичное развитие концепции домашней 3D-печати. Как и с любыми новыми идеями, цены на готовые устройства великоваты, но у умельцев всегда есть возможность построить экструдер собственными руками. Благо, что чертежи всех перечисленных устройств были выложены в открытый доступ. Конечно же, экструдеры – не панацея. Наряду с заманчивым экономическим потенциалом стоит учитывать и технологические тонкости домашнего производства. Не все виды пластика поддаются переплавке: тот же PLA проще выбросить, чем переработать. Кроме того, самодельный пруток даст достаточно большой процент брака, а многократная переработка даже подходящего пластика неминуемо приводит к его деградации.
Тем не менее, использование свежих гранул с подмешиванием переработанного пластика может вылиться в существенную экономию расходов на печатные материалы.
Статья подготовлена для 3DToday.ru
Еще больше интересных статей
Бесплатный онлайн конвертер 3D-моделей
Подпишитесь на автора
Подпишитесь на автора, если вам нравятся его публикации. Тогда вы будете получать уведомления о его новых статьях.
Отписаться от уведомлений вы всегда сможете в профиле автора.
3D-печать и высокая мода – эксклюзивное интервью с российским кутюрье
Подпишитесь на автора
Подпишитесь на автора, если вам нравятся его публикации. Тогда вы будете получать уведомления о его новых статьях.
Отписаться от уведомлений вы всегда сможете в профиле автора.
Новые алгоритмы позволяют пользователям экономить время и материал для 3D-печати
Подпишитесь на автора
Подпишитесь на автора, если вам нравятся его публикации. Тогда вы будете получать уведомления о его новых статьях.
Отписаться от уведомлений вы всегда сможете в профиле автора.
Комментарии и вопросы
Приветствую!Идея креативная и....
Можете поделиться файлом для п...
Протаскиваю с трудом, бывает н...
Добрый день. Подскажите все та...
Друзья, печатал ли кто то этим...
Здравствуйте, стал выбор между...
Доброго времени суток!Подскажи...