3.14D принтер.
Этот обзор будет про FDM принтер, часть решений в котором противоречит представлениям о правильном принтере.
Кроме того, я расскажу про свой личный опыт поиска ответов на некоторые вопросы FDM печати, в том числе те, которые время от времени задают на сайте.
Сразу хотел бы сказать, что 3D печатью я занимаюсь достаточно давно, но печатаю в основном только технические детали, которые проектирую сам и не печатаю на заказ.
Я не зарабатываю на 3D печати, и иногда запускаю на печать что-нибудь не очень нужное, просто, чтобы понаблюдать за интересной работой принтера.
Поэтому выбирая:
Закрытый или открытый принтер.
Я выбираю открытые. В них своими глазами можно увидеть процесс построения модели со всех сторон, во всех деталях и нюансах. В закрытых моделях, даже с прозрачными стенками, не всегда это удобно.
Помимо праздного созерцания, это имеет и практический смысл. Наблюдая непосредственно за процессом печати, в некоторых случаях, можно понять механизм появление тех или иных дефектов. Впрочем, конечно, далеко не все дефекты можно детектировать простым наблюдением.
Разумеется, у открытых принтеров большой минус - это сложность или невозможность печати крупных деталей пластиками с большой усадкой. А это, к сожалению, почти все, так называемые, инженерные не армированные пластики.
Впрочем, задирая температуру стола, не очень крупные детали вполне можно печатать и такими пластиками.
С другой стороны, в открытых принтерах, ремни и двигатели работают в более щадящем температурном режиме. Ну если только мы их не сравниваем с достаточно дорогими моделями, где пространства печати и механизмов разделяются.
Для своего нового принтера я взял готовый Flyingbear Tornado 2 Pro, а это частично закрытый принтер (верх открыт):
И снял все панели. В результате получился каркасный, открытый:
И это первый мой отход от "традиций".
В большинстве случаев люди, как раз рассказывают про разные пути создания именно закрытых решений. Впрочем, панели ни куда не делись и в любой момент могут вернуться на место. Но пока такой потребности не возникало.
Зато возникла потребность заменить родной, постоянно торчащий держатель катушек:
На самодельный убирающийся:
Кстати, тут ещё есть пространство для творчества и его можно сделать вообще не выступающим за пределы каркаса, жёсткость которого, вполне позволяет вешать на него катушки весом до нескольких килограмм, без заметных деформаций. Но жёсткости, конечно, много не бывает. И я бы не отказался иметь и побольше.
Толщина стали каркаса с покраской 1.65 мм.
Но жёсткость принтера не является единственным показателем его качества.
Ранее я писал, что в основном печатаю технические модели. Иногда они имеют тонкие стенки, шириной 1-2 линии экструзии. И они должны быть прочными. А для этого нужно обеспечивать хорошую свариваемость при печати.
Вот результат правильной печати. На сколе детали видно, что она получается практически литая:
При такой печати и деталь из одной-двух стенок тоже будет крепкой. Но идти к такому результату пришлось долго.
В начале своего 3D печатного пути у меня были те же проблемы, которые часто встречаются и сейчас в вопросах на этом портале - не свариваются периметры, дуршлаг вместо заполнения и т.д.
Если мы не говорим про сбои в слайсере и люфты механики, то причина этих проблем на самом деле одна - пластика поступает меньше, чем должно поступать.
А вот почему пластика поступает меньше, тут причин уже несколько.
1. Указанный в слайсере диаметр прутка пластика не соответствует реальному.
2. Не откалибрована механика передвижения каретки/стола (или нулевой уровень стола).
3. Не откалибрована подача пластика.
4. Пластик из сопла выходит не синхронно командам его подачи.
С первым пунктом всё просто - в слайсере всегда нужно указывать реальный диаметр прутка.
По второму, пункту тоже достаточно всё просто. Если вы дали команду переместить головку или стол на 100 мм, то они должны в реальности проехать именно столько. Если они проедут больше, то разумеется выдавленный пластик не займёт всё пространство и слои/периметры будут иметь зазоры или плохое сцепление друг с другом.
То же касается и третьего пункта. Если вы послали команду выдавить 100 мм прутка, то должно выйти именно столько. Если выходит меньше, то слои/периметры будут иметь пластика меньше рассчитанного количества, а соответственно будут иметь зазоры или плохое сцепление друг с другом.
Но тут есть важный нюанс, о котором нечасто или почти нигде не говорят. Попробуйте откалибровать свой экструдер. Убедитесь, какой вы молодец, подав команду выдавить 100 мм прутка и получив в реальности 100 выдавленного.
А теперь сделайте то-же самое, но на скорости в 3-5 раза больше или меньше той, на которой калибровали. Думаю многие удивятся результатам. Количество продавленного прутка будет ощутимо меняться. А что это означает? А означает это то, что там где пластик давится на большей скорости, он давится с бОльшим усилием и его будет в реальности поступать меньше. В результате могут возникнуть не сваренные или плохо сваренные участки. А там, где скорость будет меньше, наоборот, могут возникнуть наплывы, из-за большего потока.
Поэтому для калибровки потока не нужно откручивать сопло. Калибровать нужно в условиях, приближенных к рабочим.
Ну и это ещё не все проблемы.
Дело в том, что разные по эластичности пластики, даже на одной скорости будут давать разный результат.
Почему такое возникает? Возникает это из-за несовершенства проталкивающих пруток механизмов.
Поэтому, очень важно, какой на вашем принтере
Экструдер.
Я крайне рекомендую проталкивающие механизмы с несколькими ведущими и цепляющими пластик шестерёнками. Причём, чем их больше, тем меньше зависимость изменения потока от скорости этого проталкивания.
В Flyingbear Tornado 2 Pro был экструдер Titan:
Там всего одна шестерня с цепляющими пруток насечками. И я его заменил, на экструдер такого типа:
Здесь две шестерёнки, цепляющие насечками пруток, и они обе ведущие.
Этот экструдер тоже не даёт идеальной равномерности подачи при изменении скорости и/или типа пластика. Но всё же он ощутимо лучше титана.
Ну и у нас остался последний фактор, влияющий на качество сваривания пластика - несинхронность реального выдавливания с подачей команды на это выдавливание.
О чём это и почему такое происходит?
Дело в том, что пластик это не бетонный столб и при попытки его продвинуть экструдером для выдавливания в сопле, он под действием этой нагрузки изгибается, сжимается и пружинит. Причём эти явления зависят от следующих моментов:
1. От эластичности пластика.
2. От лёгкости прохождения через сопло, что в свою очередь зависит от его (сопла) диаметра, длины и нагрева.
3. От длины между механизмом проталкивания и соплом.
4. От зазора между прутком и подающей трубкой.
Очевидно, что использовать только жёсткие пластики мы не можем, поскольку иногда бывают нужны и эластичные детали. Ставить крупные сопла для лёгкого прохождения пластика тоже не всегда возможно, как и сильно задирать его температуру.
А вот двумя последними параметрами мы вполне можем поуправлять.
Поэтому следующей, и очень важной характеристикой, является система подачи прутка.
Боуден или директ.
Очень часто, на ресурсах по 3D печати можно встретить статьи, в которых описывается борьба за каждый грамм печатающей головки, поскольку это позволяет выиграть ещё несколько мм/с2 ускорения и несколько мм/с скорости.
Это напоминает мне Формулу 1, где люди учитывают, что некоторая площадь, покрытая чёрной краской весит на 200 г меньше, чем такая же площадь белой, и это позволяет отыграть 0.001 с на круге.
В общем, серьёзная борьба серьёзных пацанов за скорость. А кто-нибудь задумывался, влияет ли это увеличение скорости на качество сваривания пластика или нет?
Я задумался и провёл достаточно много экспериментов на эту тему. И могу точно сказать, что свариваемость с увеличением скорости существенно падает.
На самом деле это, в общем-то, достаточно очевидный вывод. Ведь чтобы вытекающий пластик сварился с уже застывшим, застывший нужно сначала расплавить. А это гораздо лучше получается, когда горячее сопло дольше находится над застывшим пластиком, и дольше передаёт своё тепло месту соприкосновения расплавленного и уже застывшего.
В результате, когда я понял, что борьба за скорость противоречит моим критериям правильной 3D печати, мне стало гораздо легче принять решение какую систему подачи пластика использовать.
Но для начала давайте разберём плюсы и минусы обоих систем.
Боуден подача позволяет вынести тяжёлое устройство проталкивания прутка за пределы подвижной головы, тем самым уменьшает её инерционность.
Это влечёт два положительных момента.
1. Можно увеличить максимальную скорость/ускорение её передвижения при печати и соответственно уменьшить время печати.
2. При равных скоростях и ускорениях более лёгкая голова будет давать лучшее качество из-за различных резонансных и инерционных явлений.
3. Компактная голова позволяет увеличить область печати.
Но на мой взгляд, минусы боудена перекрывают его плюсы.
Из-за большой длины прутка между механизмом проталкивания и соплом, пруток там изгибается, что приводит к тому, что возникает рассинхронизация между командами на проталкивание прутка и его реальным вытеканием из сопла. Выражается это в том, что в начальный момент, когда экструдер начинает подавать пруток, он сгибается и сжимается в трубке, но из сопла ещё не выходит, а головка то уже едет и у нас в модели в этом месте получается дырка. А в конце, наоборот, экструдер останавливает подачу, но из-за изогнутого пружинящего прутка происходит продолжение выталкивания расплава из из сопла и пластик продолжает течь, в результате чего в этом месте получается наплыв.
И с увеличением размера принтера эта проблема обостряется, поскольку увеличивается длина подающей трубы, в которой пруток сжимается и деформируется.
Есть, конечно, всем известный Linear Advance, который пытается эти вещи нивелировать.
Работает он следующим образом. В начальный момент, когда пруток начинает изгибаться, он резко увеличивает его подачу, чтобы этот изгиб произошёл быстрее и началось вытекание пластика из сопла с минимальной задержкой, а в момент окончания подачи, наоборот, очень резко откатывает согнутый пластик обратно, чтобы прекратить вытекание из сопла.
Всё это конечно интересно, но это описание слишком упрощено. Ведь подача пластика в реальной печати не всегда дискретна, не только может начинаться с нуля и заканчиваться нулём, но и может меняться скорость на разных участках. И при разных скоростях с одной настройкой эта технология работает не одинаково. То же касается и разных типов пластиков. Отстроенная для одного, она не будет работать для пластика с другой гибкостью и эластичностью. Кроме того, она сама может привносить новые артефакты печати.
В общем, после кучи экспериментов, мне пришлось отказаться от неё. Убирая одни дефекты, она давала ряд других, и нянчиться с ней приходилось как с дитём малым, каждый раз подбирая под каждую деталь и каждый пластик свой коэффициент. Но на сложных деталях не помогало даже это.
Другой очевидный вариант решения основной проблемы боудена, это использовать узкие трубки подачи, почти впритык к диаметру прутка. Но это разбивается о наши реалии, когда размер прутка может скакать очень сильно. Кроме того, такая трубка создаёт большее трение для прутка, что в свою очередь ещё больше обостряет проблему - большее трение приводит к увеличению усилия проталкивания, что в свою очередь приводит к увеличению изгиба и сжатия прутка, что ещё больше увеличивает нелинейность его движения.
В общем, поиграв с такой трубкой, я от неё отказался.
В этот момент я понял, что добиться от боудена стабильности и предсказуемости на разных режимах печати и пластиках у меня не получится, поэтому очевидным решением был переход на директ.
Его я реализовал ещё на старом принтере. Но там длина прутка от механизма подачи до сопла была около 8 см. Но даже с такой длиной счастью моему не было предела. На том же самом принтере печать стала просто фантастической. Дыры между периметрами пропали сами собой. Сплошное заполнение, наконец, действительно стало сплошным, а не дуршлагом.
Ретракт удалось снизить с 7-11 мм до 1 - 3 мм(на мягких пластиках). Фторопластовая трубка перестала перетираться в фитингах и выскакивать от нагрузки.
Разумеется, на новом принтере я так же решил отказаться от боудена. И здесь моя цель была ещё более амбициозна. Я решил снизить дистанцию изгибающегося прутка ещё раза в два. Для этого был приобретён подобный вот этому экструдер:
Он одновременно является и экструдером и радиатором термобарьера, что позволяет убрать эту деталь (радиатор) и вычесть её длину из участка неизбежного изгиба/сжатия пластика.
И результат действительно стал ещё лучше. Ретракт удалось снизить до 0.5 - 1.5 мм. Я забыл, что такое сопли на PETG. И только на очень эластичных пластиках я иногда их вижу, но в гораздо меньших количествах, чем на предыдущем директе и уж тем боле на боудене.
Но чтобы установить этот директ на Flyingbear Tornado 2 Pro для него была спроектирована совершенно новая
Голова.
Родная была стальная:
И от неё осталось только несколько крепёжных пластин.
Остальная часть была спроектирована с нуля. И в ней есть ряд нестандартных и необычных решений, за которые меня возможно, в комментариях пожурят. Но она работает. Это факт.
Итак, вот она:
Попытаюсь объяснить все странные, на первый взгляд решения, которые в ней присутствуют.
Первое, что очевидно, она не маленькая. Но директ, собственно, совсем маленьким и не бывает, это ожидаемо. Но вот почему я не использовал низкие двигатели-блинчики?
На самом деле я их использовал в прошлом принтере. И результат мне совсем не понравился.
Греются как кипятильник, даже с радиатором, а силёнок всё равно не хватает.
Поэтому в этом принтере решил поставить двигатель побольше. Причём по размеру это получилось не намного больше, чем блинчик с радиатором. Вес, да, он конечно больше. Но зато у этого движка нет проблем, ни с усилием, ни с перегревом.
Но меня волновало, что такая длинная голова может приводить к угловым колебаниям относительно крепления. Но результат оказался очень хорошим - линейный направляющие хоть и нонейм, но люфтов нет и голова не болтается. А кроме того, сопло находится ближе к каретке, что тоже уменьшает его возможное раскачивание.
В общем, при печати никаких проблем с этим нет.
Следующее, что я думаю все заметили, это громадный, относительно обычно используемых, 60 мм вентилятор охлаждения радиатора термобарьера. Собственно конструкцию я разработал так, что он охлаждает не только экструдер-радиатор, но и двигатель.
Обратите внимание, у экструдера с обеих сторон есть зазоры для прохода воздушного потока и улучшения охлаждения.
Такая конструкция позволила создать эффективное охлаждение и при небольших оборотах. При этом вентилятор работает даже не на полную мощность, благодаря регулятору напряжения:
В результате мы имеем не звенящий 30-40 мм вентилятор, который в любой момент может умереть от своих бешенных оборотов, а малооборотистый, тихий и более надёжный 60 мм.
Конечно и маленькие можно купить качественные и надёжные, но очевидно, что при прочих равных, менее оборотистый будет надёжнее.
Рассматривая голову дальше, обратите внимание на прозрачную трубку подачи пластика, подходящую к ней. Это фторопластовая, но не обычная белая, а прозрачная трубка. Поверьте, это очень удобно видеть, что в ней происходит.
Кроме того, её внутренний диаметр 3 мм, а не 2 мм, что снижает в ней трение, несколько облегчая работу экструдеру.
Ну и крепится всё описанное выше на пластиковом каркасе, распечатанным из... PETG.
Странное или даже глупое решение. Там же совсем рядом очень горячий хотэнд, а PETG очень легкоплавкий пластик.
На самом деле ситуация тут в том, что PETG легко печатается на открытых принтерах, и у меня его много. Поэтому этот каркас был тестовый экземпляр для оценки работоспособности общего решения головы.
А решение оказалось удачным (на мой взгляд), а с PETG каркасом за длительное время так ничего и не случилось, и он остался жить в принтере и дальше. Неожиданно, но факт.
Возможно, этому помогает правильно разработанное охлаждение и обмотка алюминиевого нагревательного блока термостойкой фторопластовой лентой:
Но думаю многих, уже некоторое время интересует вопрос, как же такая здоровая голова может ездить, и может ли она ездить вообще :) ?
Потянет ли её, существующая у Flyingbear Tornado 2 Pro
Кинематическая схема.
У этого принтера она классическая. Каждая ось гоняется своим приводом. В результате привод оси Y:
гоняет ось X вместе с балкой и двигателем X:
Ну и большой головой на ней. Но важный момент - ремни у этого принтера 10 мм, а не 6 мм, и стоят мощные 48 мм двигатели на осях X и Y. А на оси Y их даже два (за всё время работы рассинхрона между ними не было):
В результате этот принтер умеет двигать осями X и Y со скоростью 300 мм/с на ускорениях 3000 м/с2.
Разумеется, на такой скорости я не печатаю. Но я её использую для быстрого холостого перемещения при печати, для минимизация вытекания пластика и образования, так называемых, соплей. И это действительно помогает.
В результате получается, что для быстрых перемещений совсем необязательно иметь CoreXY или H-Bot кинематику. Ну и в этом случае мы избегаем их неприятных особенностей, связанных с перекашиванием балок или слишком длинными, перекрещивающимися ремнями.
Но для быстрого перемещения не достаточно правильной и мощной механики. Мозги у принтера тоже должны быть шустрыми, чтобы в сложных условиях не подтормаживать, и не создавать локальных непонятных и плохо объяснимых дефектов.
Для этого нам нужна хорошая
Плата управления.
В этом принтере она 8-ми битная MKS GEN_L:
Как и на моём старом. Но старый принтер медленнее, поэтому здесь я решил заменить MKS GEN_L на BigTreeTech SKR V1.3:
Это уже 32 битная недорогая плата управления, на которую я залил прошивку Marlin 2.0.
Честно скажу, каких-то явных улучшений я не увидел, хотя возможно они и есть. Но было интересно изучить прошивку, чтобы сконфигурировать её под конкретный принтер. Узнал много интересного.
В частности, что делать, если плохо ШИМится
Вентилятор охлаждения детали.
Родная система охлаждения печатающихся деталей была сама напечатана на 3D принтере и включала маленький гудящий вентилятор.
Вентиляторы этой фирмы у меня дохли на старом принтере раз в три месяца при совсем небольшой временнОй рабочей нагрузке.
Ну и вообще, если честно, мне не совсем понятен принцип такого охлаждения, когда воздух дует в район сопла. Для нормального сваривания пластик должен прогреться. Поэтому охлаждаться должна часть детали, с которой сопло уже съехало и процесс сваривания закончен.
Ну и кроме того, мне не нравятся классические схемы охлаждения тем, что они закрывают сопло.
А мне уж очень нравится наблюдать за самим процессом печати.
И я опять пошёл своим путём. Ожидаю ваши тапки в комментариях в мой адрес:
Да, это здоровый, 120 мм, мощный вентилятор, дующий на весть стол.
Но эта схема работает. Она, в большей степени, дует на части детали, где нет головы, охлаждая именно то, что уже не находится в процессе сваривания. Точнее дует то она везде, но общую интенсивность можно снизить, поскольку участки вне точки печати обдуваются дольше, чем сама точка печати.
Конечно, у такой системы есть и серьёзные недостатки.
Она сильнее охлаждает стол, что может приводит к отклеиванию детали.
С противоположной стороны потока деталь, всё-таки, может перегреваться. При этом встречное расположение вентилятора не улучшает ситуацию, а ухудшает. Что, если задуматься, логично - встречные потоки создают некую область застоя воздуха.
Я даже хотел использовать дым, как большие ребята в аэродинамической трубе, для изучения воздушных потоков и проектирования более качественного обдува.
Но пока забил на это, поскольку приемлемое качество всё же такой обдув даёт.
Ну и плюс он тише мелких турбин, располагающихся на голове.
Кроме того, этот вентилятор у меня включается по окончании печати на 100% мощности для ускорения остывания стола.
А вот с промежуточными мощностями, у меня поначалу возникли проблемы. На прошлом принтере таких проблем не было, там стоял дешёвый китайский вентилятор. А вот новые Sunon и Jamicon либо крутились почти на 100%, либо останавливались. Ну никак не хотели управляться ШИМом.
Проблема в том, что эти вентиляторы сильно умные. У них есть механизм автозапуска, который и портит всю малину. В частности, Sunon, но без автозапуска, управлялся нормально. Но без автозапуска у меня был только маленький.
Можно было, конечно, поставить RCL фильтр, что я поначалу и сделал. Но работа с ним меня тоже не очень впечатлила. А кроме того, его нужно рассчитывать или подбирать под конкретную модель вентилятора. А мне не хотелось привязываться к конкретной модели, поскольку на тот момент я ещё не определился ни с необходимым размером, ни с количеством вентиляторов охлаждения детали.
Попытка найти преобразователь ШИМ -> напряжение не привела к успеху. Несмотря на очевидную востребованность таких плат, я так и не смог найти ничего подходящего.
Вообще, такие платы всё-таки есть, но их характеристики в плане диапазонов напряжения и нагрузочной способности не удовлетворяют поставленной задаче питания имеющегося вентилятора.
Поэтому я искал решение дальше и нашёл известный и простой путь - включить программный ШИМ Марлина, который по частоте существенно ниже аппаратного, установленного по-умолчанию. И с ним такие капризные вентиляторы могут заработать.
Включается это параметром:
#define FAN_SOFT_PWM
Это тоже не идеальное решение - вентилятор может издавать разные посторонние звуки на промежуточных скоростях. Но идеального я пока так и не нашёл.
Кроме того, имеет смысл включить параметр:
#define FAN_KICKSTART_TIME 300
Если вентилятор не стартует на низких оборотах, но может поддерживать на них вращение, то этот параметр будет спасением. В нём задаётся время в мс, на которое вентилятор запускается на 100% мощности.
Это приводит к его успешному старту, а дальше он уже вращается на заданной скорости.
Ну и раз мы заговорили про охлаждение, хочу показать свой вариант охлаждения драйверов шаговых двигателей.
Обычно эти драйверы с радиатором выглядят так:
Алюминиевый радиатор через теплопроводную самоклейку лепится на пластиковый корпус чипа.
Мало того, что самоклейка при нагреве может ползти и в результате радиатор может коротнуть элементы платы, а это как правило, заканчивается эффектным фейерверком, так ещё и расстояние от радиатора, до токопроводящих частей элементов платы, находящихся под ним, иногда достигает ну прям реально сотых долей мм.
Мне это совсем не нравится. Вероятность выгорания драйвера, вслед за ним платы управления, и возможно компьютера, через который я обычно произвожу печать, меня совсем не прельщала.
Поэтому я решил немного модернизировать систему охлаждения, а заодно и избавиться от вентилятора обдува радиаторов драйверов.
Модернизация заключается в следующем. Вырезается из нетолстого алюминия или меди квадрат по размеру корпуса чипа. Приклеивается к нему этот квадрат теплопроводящим клеем. А уже к нему приклеиваем более крупный радиатор. Таким образом мы приподнимаем радиатор над элементами платы и избегаем КЗ. Также рекомендую не жалеть клея и хорошо им залить всё вокруг. Ноги микросхемы являются хорошим теплоотводом, поэтому залив клеем и их, вы улучшите отвод тепла от чипа.
Так же обратите внимание на два относительно крупных резистора рядом с чипом:
По моему расчёту они не предназначены для пассивного охлаждения. Поэтому, если вы тоже не планируете использовать вентилятор для охлаждения драйверов, эти резисторы также следует залить клеем вместе со всем остальным:
Реальная эксплуатация показал, что это решение вполне рабочее. Пропуска шагов, выгорания драйверов за уже относительно длительный срок эксплуатации принтера не было.
Но почему я стал использовать эти старые, древние шумные
Драйверы.
Родные были TMC 2208. Ещё одно странное решение. Заменить Мерседес на трактор.
Но ситуация очень простая. TMC 2208 на больших скоростях и ускорениях просто зависают.
Это старый известный и почему-то упорно неисправляемый глюк. На самом деле решение есть, это перевод их из режима stealthChop в spreadCycle. Но на момент переделки принтера я этого не знал.
Кроме того, эта переделка режимов несколько увеличивает громкость работы шаговиков.
Но лично я не пробовал это делать и не могу оценить получающийся результат.
Кому интересно, могут поискать дополнительную информацию по указанным выше ключевым словам.
В том же виде, в котором TMC 2208 были у меня, они проигрывали A4988 в стабильности работы вчистую.
При средних скоростях и бОльшем, чем у A4988 токе, TMC 2208 пропускали шаги. А на высоких скоростях, как я уже и сказал, просто тупо зависали. Причём все четыре вели себя абсолютно одинаково и на всех осях.
Так что пришлось вернуться к старым, шумным, но проверенным, мощным и надёжно работающим A4988.
Но со временем, я всё же попробую их заменить на что-то более тихое, чтобы ничего не шумело, как, например,
Блок питания.
Родной БП 24 В, 600 Вт, мощный:
Сделан внутри и снаружи аккуратно, но шумноват. Формфактор у него обычный, легко разбирается для замены вентилятора на более тихий ну и более надёжный. Поставил Sunon HA60151V4-A99. С учётом регулировки оборотов блоком питания в зависимости от температуры внутри корпуса, получилось очень тихо.
Такой мощный блок питания нужен, чтобы греть относительно крупный
Стол.
Он квадратный, имеет размер 360 х 360 мм, на поверхности какое-то адгезивное точечное покрытие:
Переделка на директ несколько снизила область печати до 332 х 335 мм.
Высота печати осталась почти родная - 370 мм.
Провода нагревателя и термистора стола сразу заменил на сверхгибкие силиконовые, заодно их приклеил к столу силиконовым же нейтральным герметиком:
С одной стороны провода понравились - много мелких жил, в результате провод действительно мягкий и гибкий.
Изоляция так же честный силикон, от паяльника не плавится. Но вот качество этого силикона просто никакое - разваливается от лёгкого нажатие ногтем.
Двигается стол по четырём валам.
Привод - два винта с шаговым двигателем на каждом:
За всё время работы рассинхрона между ними и соответственно перекоса стола не было. Включил я их, как и двигатели оси Y, последовательно.
Что порадовало, так это то, что наконец, с точки зрения механики, привод стола сделан верно.
Двигатели с муфтами вверху. А внизу упорные подшипники. В результате вес стола давит как раз на упорные подшипники, которые для этого и предназначены. И не давит на муфту и двигатель, которые для этого не предназначены:
Дальше сделано уже не так всё хорошо, как хотелось бы.
Алюминиевый лист стола тонкий, но к нему прочно приклеено стекло:
В результате стол получился достаточно ровным.
Но не съёмным. Снимать напечатанные детали может быть не очень удобно.
Кроме того, такое покрытие со временем облезет. И чтобы не ждать этого чудесного момента и не ломать голову, что делать дальше, я просто положил на него лист зеркала, на котором и печатаю.
Конечно, на первый взгляд, такое решение кажется, мягко говоря, странным. Но, а как здесь поступить по-другому? Отдирать родное стекло со 100% вероятность погнуть тонкий лист алюминия, и получить вместо ровной поверхности барханы?
Кончено, температура на поверхности верхнего стекла в таком решении существенно отличается от показаний датчика. Но печати это совершенно не мешает. Всё равно параметры подбираешь для конкретных ситуаций и дальше это уже просто абстрактные цифры.
Ну и к тому же литое стекло, как оказалось, не такой уж и плохой проводник тепла.
По поводу абсолютных значений нагрева точно не могу сказать, но поверхность достаточно прогревается для печати ABS пластиком не очень крупных деталей, и это с учётом того, что принтер открытый.
Но такое решение имеет и существенные плюсы. Теперь можно зеркало спокойно снять со стола, чтобы было проще отделить въевшуюся в него деталь, или положить в холодильник, чтобы сама отвалилась.
Да и наносить адгезив, особенно спрей, так гораздо удобнее и безопаснее для механизмов принтера.
Кстати, возможно не все знают, но средства для адгезии, являются и средствами от адгезии.
Как-то, начитавшись красивых историй про печать на чистом стекле, решил попечатать так и сам.
Но после нескольких, выдранных вместе с деталью кусков стекла из стекла, я решил, что это не моё, и лучше уж я буду использовать адгезивы, которые позволяют при остывании снимать детали без повреждений.
А вот качественно липнуть, помимо адгезивов, помогают беспрецедентная ровность стола, благодаря двум слоям стекла, правильная установка нуля и стабильно срабатывающие
Концевики.
Концевик Z был ёмкостным, и поэтому реагировал и на не металлические поверхности, в том числе и стекло. Это плюс. А минусы - его стабильность срабатывания была не очень высокой, и он располагался на голове и мешал обзору области печати. В общем, я его снёс без сожаления.
Расположение на голове, конечно, позволяло строить карту неровностей стола и корректировать эту неровность. Но стол, как я уже и сказал ровный, поэтому достаточно было совместить его плоскость с плоскостью передвижения головки. По старому принтеру знаю, что операция эта делается раз и дальше этого хватает надолго. И не надо дрыгать осью Z, пытаясь выровнять кривое. И всё равно ведь оно кривым и останется.
В общем заменил концевик Z на стационарный индуктивный:
В них, на удивление, очень высокая стабильность расстояния срабатывания, даже при изменении напряжения питания.
Заодно заменил такими же и микрики-концевики X(на голове) и Y:
В плане точности для этих осей такие датчики избыточны, достаточно было и микриков. Но мне не хотелось механического контакта в концевиках по двум причинам. Первая причина - меньшая надёжность. Для сравнения, на фото контакт старого окислившегося и нового микрика:
Вторая причина - чтобы не сломать их относительно мощной механикой, если что-то пойдёт не так.
Как альтернативу, можно было рассмотреть оптические концевики. Но пыль в открытом принтере и солнце из окна вряд ли делали такой выбор разумным.
Впрочем, я готов к экспериментам, поэтому сделал не совсем обычный
Блок управления.
Родной - это стальная коробка, в которой всё было напихано впритык.
Доступ к отдельным компонентам представлял собой нетривиальную задачу.
Но принтер задумывался как полигон для экспериментов, поэтому мне была нужна лёгкая доступность всех элементов электроники для их замены или доработки.
Поэтому было придумано, опять-таки, не совсем обычное, но очень удобное для поставленных целей решение:
Не очень аккуратно, но оно позволяет, во-первых, освободить видимую часть принтера от проводов:
А во-вторых, позволяет легко размещать дополнительные устройства или перемещать имеющиеся.
В частности, я планировал дополнительно здесь разместить:
Плату мониторинга состояния принтера.
Преобразователь ШИМ -> напряжение, для качественной регулировки оборотов вентилятора.
Возможно, дополнительный регулятор напряжения, для питания обдува платы управления, если пассивного охлаждения всё-таки будет не достаточно.
Элементы управления и питания подсветки.
Фотоэлемент для регулировки яркости индикации и подсветки, в зависимости от внешнего освещения.
Больше всего мне, конечно, хотелось сделать плату мониторинга состояния принтера, независимую от платы управления.
Для начала, предполагал контролировать с её помощью несколько параметров:
Соответствие реального протягивание прутка поданным для этого протягивания командам - для определения проблем с подачей.
Температуры ключевых элементов - для детекции предаварийных и аварийных состояний.
Режим работы принтера - нормальная печать, ожидание прогрева стола/сопла, окончание печати, беспричинная остановка механизмов во время печати и тд.
Выводить собранную ей информацию планировал на
Устройство индикации.
Родное, это цветной, резистивно-сенсорный экран, позволяющий управлять принтером и отображать режимы его работы:
Вайфая у меня в принтере не было.
В их связке с родной же платой управления были какие-то проблемы. Что-то с питанием, и работали они очень глючно. Но глубоко разбираться я не стал, поскольку всё равно планировал заменить их обоих.
Печатаю я всегда с компьютера по USB, мне так удобнее. Для безопасности компьютера, в какой-то момент, я решил использовать такое устройство:
Это гальваническая USB развязка ADUM4160.
Она развязывает и шины данных и питание. Изолирующая способность - несколько киловольт.
Внутри установлен маломощный преобразователь напряжение с гальванической развязкой входа и выхода, который питает специализированную микросхему гальванической развязки линий данных и остаток мощности выдаётся на выход. Впрочем, выходное напряжение нам и не нужно, плата управления его не использует, ей достаточно линий данных.
Ну и поскольку печать и управление принтером идёт с компьютера, то родная плата экрана мне не нужна и была заменена на RGB светодиод, для отображения текущего экспресс-статуса принтера:
К сожалению, руки до построения платы мониторинга состояния принтера, включая необходимые для этого датчики, у меня так и не дошли. И светодиод пока показывает только один статус - зелёный, т.е. всё хорошо.
А убедиться действительно ли всё хорошо с этим принтером или нет, мы можем посмотрев
Примеры печати.
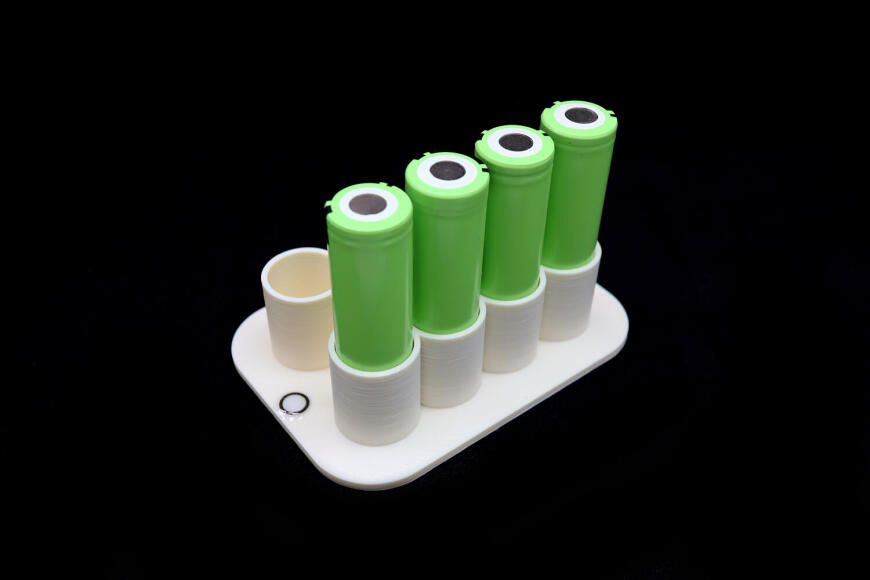
Обратите внимание, ABS пластик, открытый принтер, не самая маленькая деталь, но дно абсолютно ровное:А вот и полный комплект:
Коробочка:
Противопылевая заглушка розетки 220 В:
Колпачок для тюбика клея Момент, взамен родного развалившегося:
Крепление бинокуляров:
Ручки для самодельных шестигранных отвёрток:
Подставка и крышка (взамен сломавшейся) под китайскую эпоксидку:
Крепление объектива сканера на фотоаппарат:
На него я делал обзор и второй обзор.
И с его помощью сделаны фото контактов микриков, которые я приводил чуть выше.
Вот ещё несколько примеров его работы.
Шарик пишущего стержня:
Ну и на этом у меня всё, всем пока!
Еще больше интересных статей
Anycubic Photon Mono M7 — подробный разбор флагманской линейки фотополимерных принтеров
Подпишитесь на автора
Подпишитесь на автора, если вам нравятся его публикации. Тогда вы будете получать уведомления о его новых статьях.
Отписаться от уведомлений вы всегда сможете в профиле автора.
LCD - принтеры HeyGears Reflex и Reflex RS: новинка на российском рынке
Подпишитесь на автора
Подпишитесь на автора, если вам нравятся его публикации. Тогда вы будете получать уведомления о его новых статьях.
Отписаться от уведомлений вы всегда сможете в профиле автора.
Практика использования лазера мощностью 5,5Вт
Подпишитесь на автора
Подпишитесь на автора, если вам нравятся его публикации. Тогда вы будете получать уведомления о его новых статьях.
Отписаться от уведомлений вы всегда сможете в профиле автора.
Комментарии и вопросы
Вероятно потому, что у некотор...
Нет, уголовки за пневму выше 7...
Почему попрежнему нет CAM для....
Тонкая стенка.Видите между дву...
Привет всем. Имею принтер Ende...
Перестал грузиться Trumpf buil...
В один момент стало печатать в...